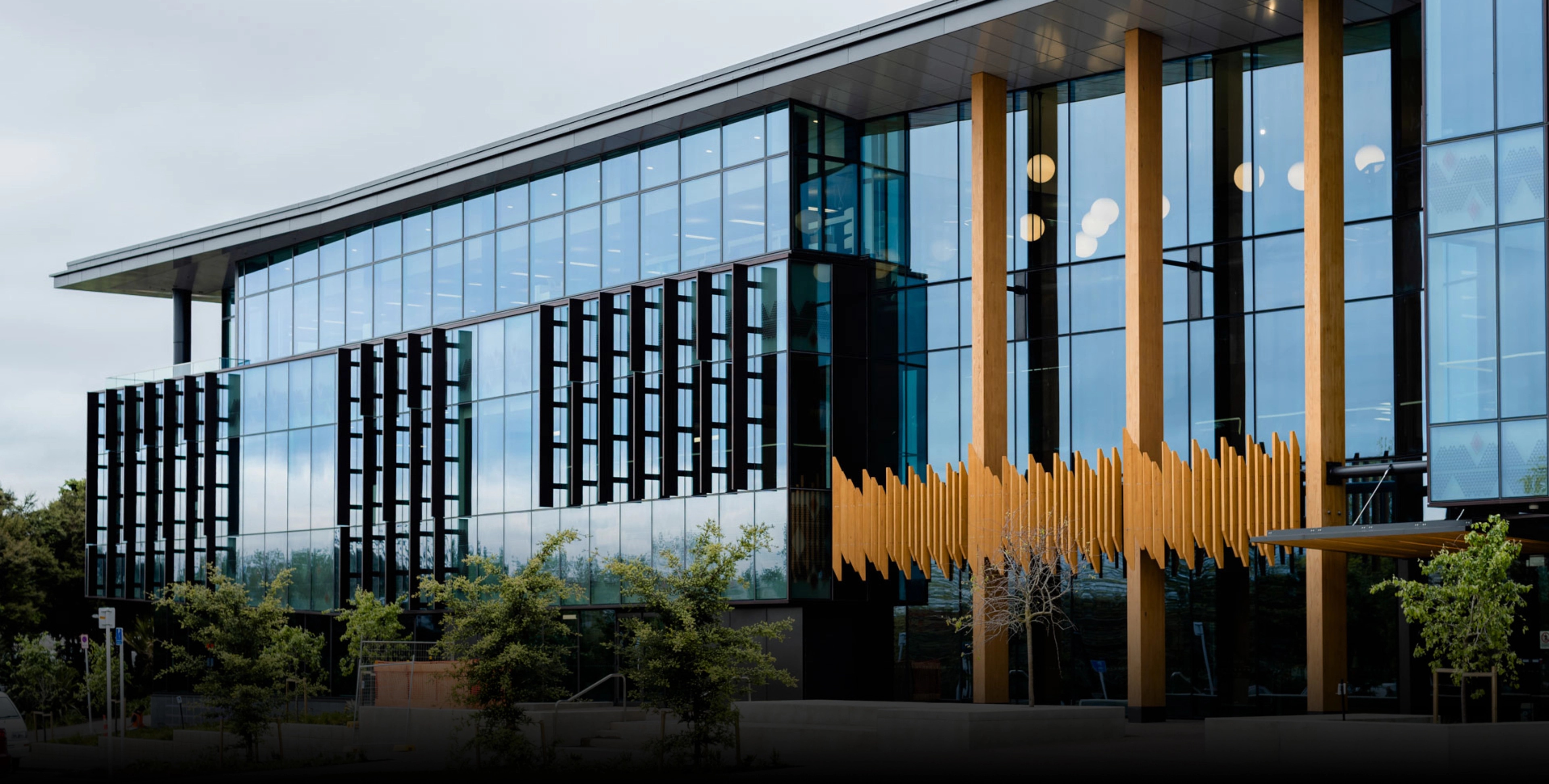
Massey University Innovation Complex
Massey University’s focus on research and innovation is exemplified in their new Innovation Complex, a four-level facility housing labs, teaching areas and multipurpose spaces for a wide range of science and technology disciplines.
Befitting the technologically advanced nature of the building, construction methodologies have also been future-forward.
To deliver on the complexities of building to ‘medical grade’ building we used building information modelling (BIM) to view the project in virtual reality 3D; this allowed us to front-foot and resolve issues without compromising on delivery excellence; essentially ensuring key installations were done once and done right.
Key information
Client: | Massey University |
Dates: | September 2019 - October 2022 |
Total value: | $110M |
Area: | 10,000m2 |
Design: | Athfields Architects |
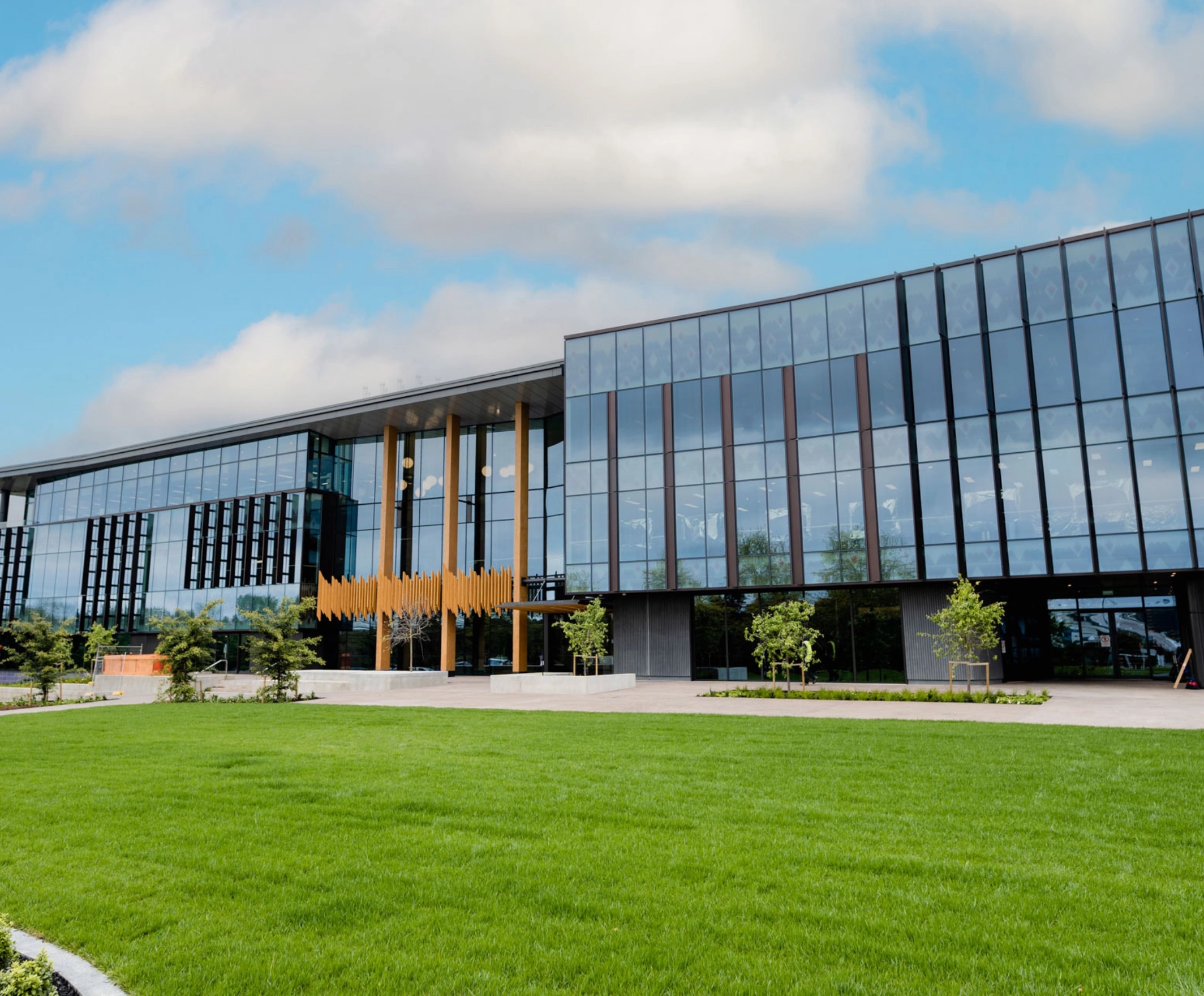
Watch case study video here
About the project
This project encompassed design, consents, BIM milestones, and all construction works. The first stage involved the construction of a bus lane, footpath, and installation of foundation beams comprising 77 bored piles.
The second stage was the main build, involving construction of a four-level building with 10,000m2 of laboratories (60%) and teaching spaces (40%).
The facade of the building is a combination of aluminium and glass curtain wall.
In terms of building and service complexity, this facility is comparable to a hospital. It contains precision positive and negative air pressure HVAC systems to furnish PC3-level laboratory requirements; medical gas infrastructure and supply; complex electrical supply and building management systems; a state of the art fibre optic data system; and the latest smart teaching technology.
The acoustic requirements between rooms and floor levels meet the high specifications required for teaching, together with the unique internal fire separations - similar to those required in an apartment complex.
Our approach
Our dedicated project BIM Co-Ordinator and Building Services Manager used 3D modelling to co-ordinate clash detection and provide a common platform for successful design and construction. As a result, construction clashes were almost negligible. In addition to traditional QA processes, our team used smart technology to QA building element locations in real time - further enhancing the contribution that BIM co-ordination made.
We were able to ensure that buildability, product selection and innovative building sequences were all considered ahead of construction commencing. This resulted in project costs being significantly below budget. Budget was maintained during construction through cementing design and costs early on.
The build sequence was such that areas were completed sequentially - allowing completed areas to be defected far earlier than the usual end of project ‘bottleneck’. These areas were then locked to prevent access.
In parallel, our team worked on a ‘soft landing’ approach with the University, so that completed areas could be populated with laboratory equipment. This process not only assisted them in streamlining building preparation, but also provided clear defect delineation.
Key Services
Design management | |
Construction methodology advice | |
Planning and resource scheduling | |
Construction ready designs | |
Digital quality control management | |
Project scanning and capture | |
Digital asset management | |
Construction site automation |
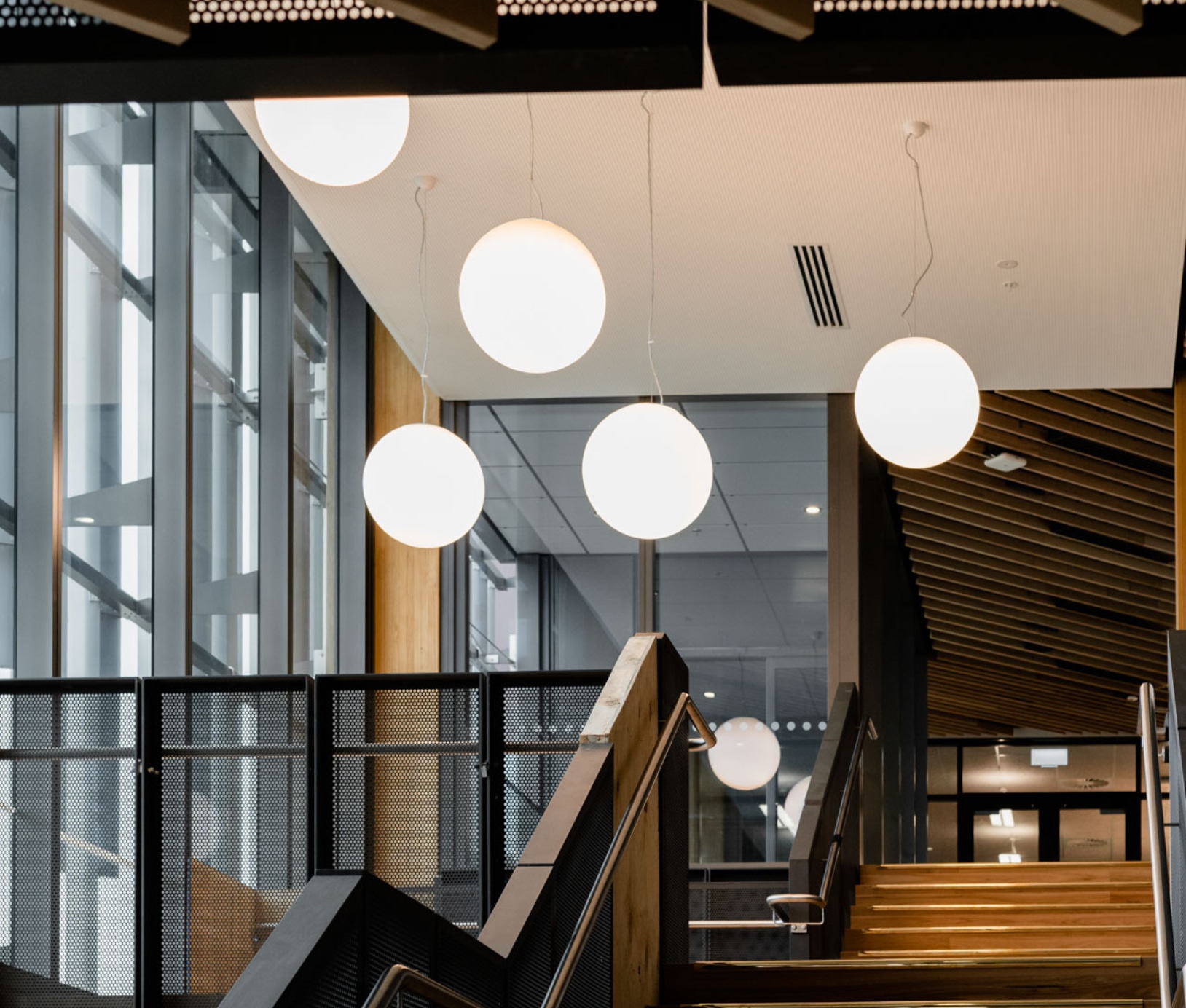
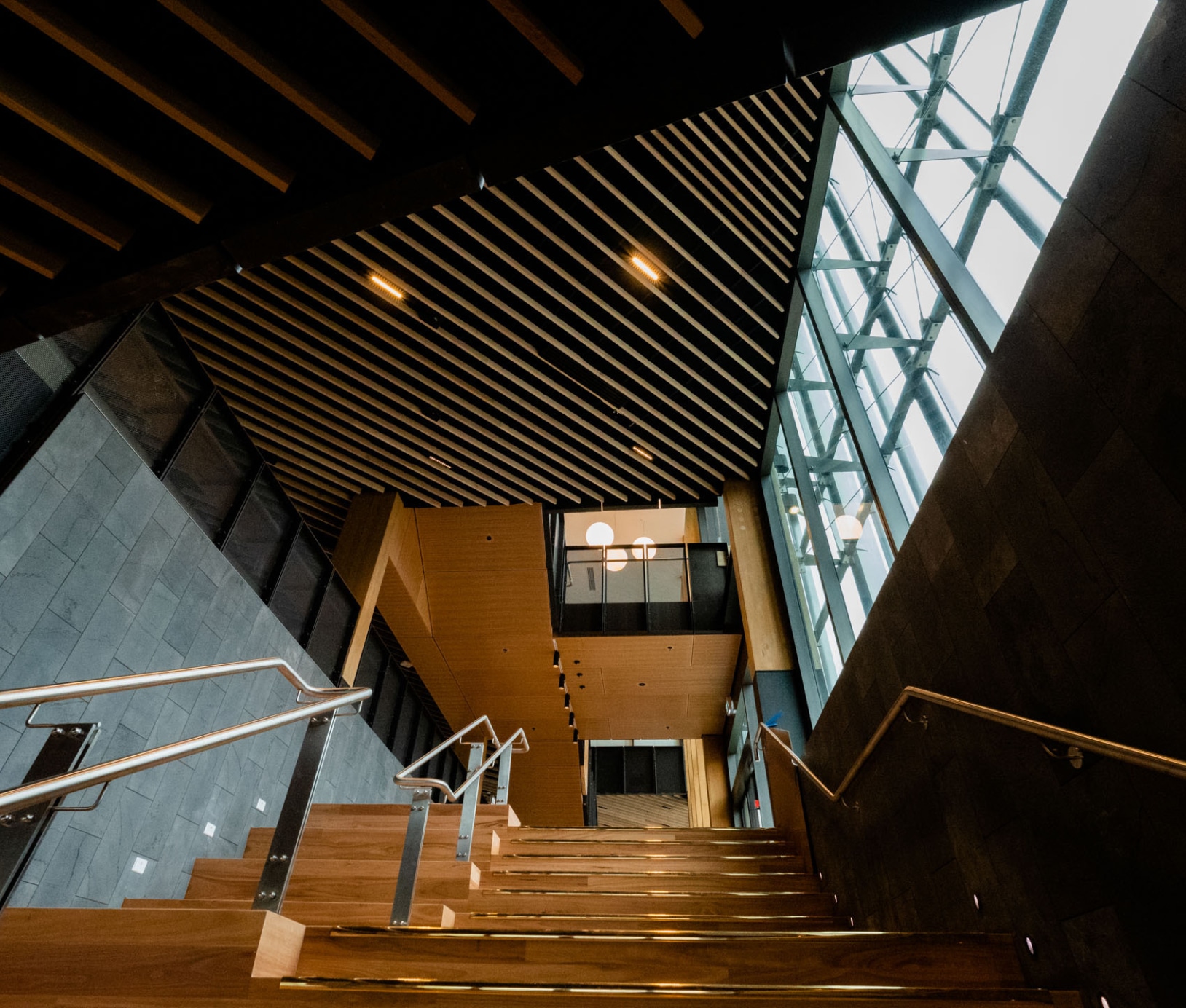
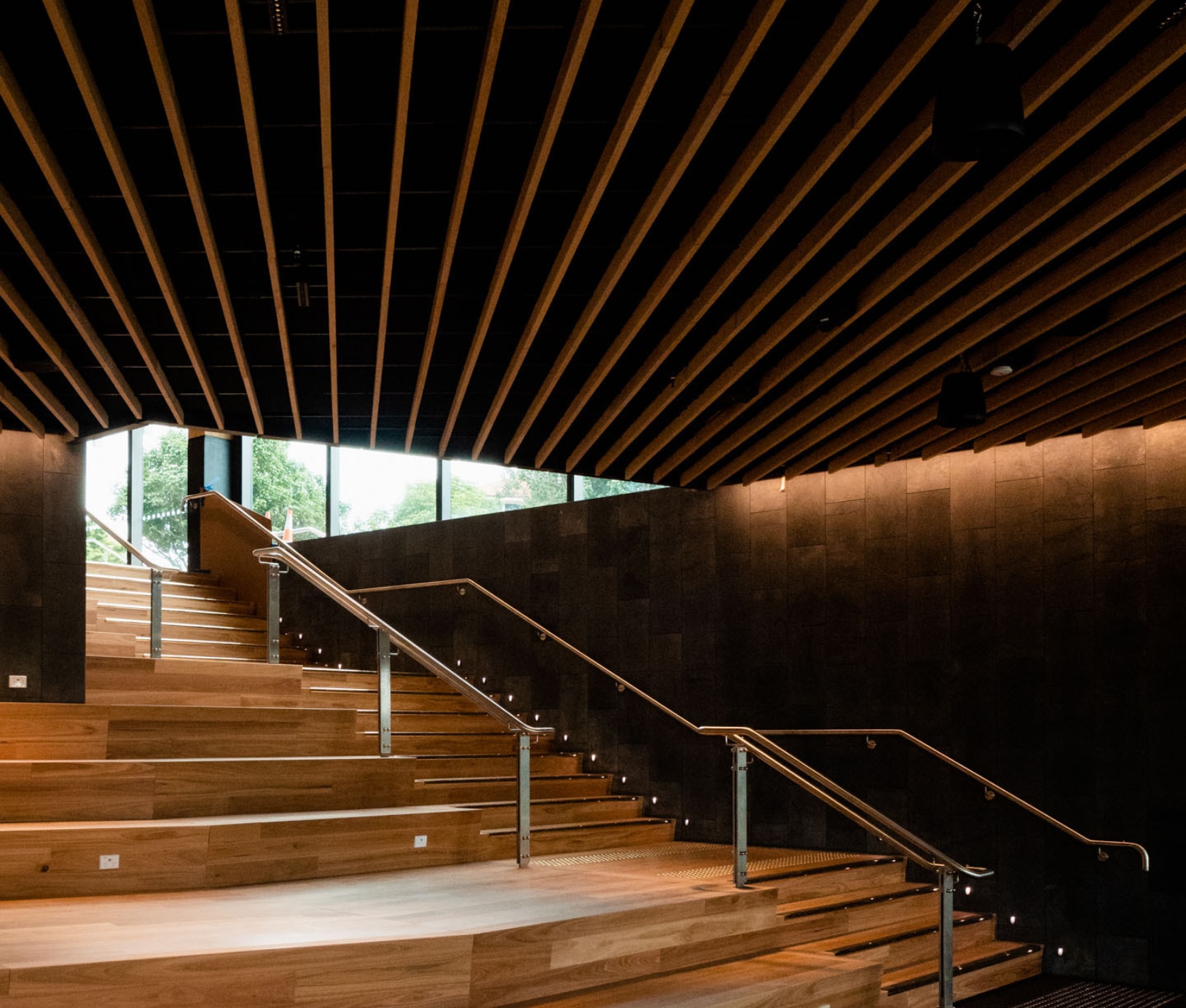
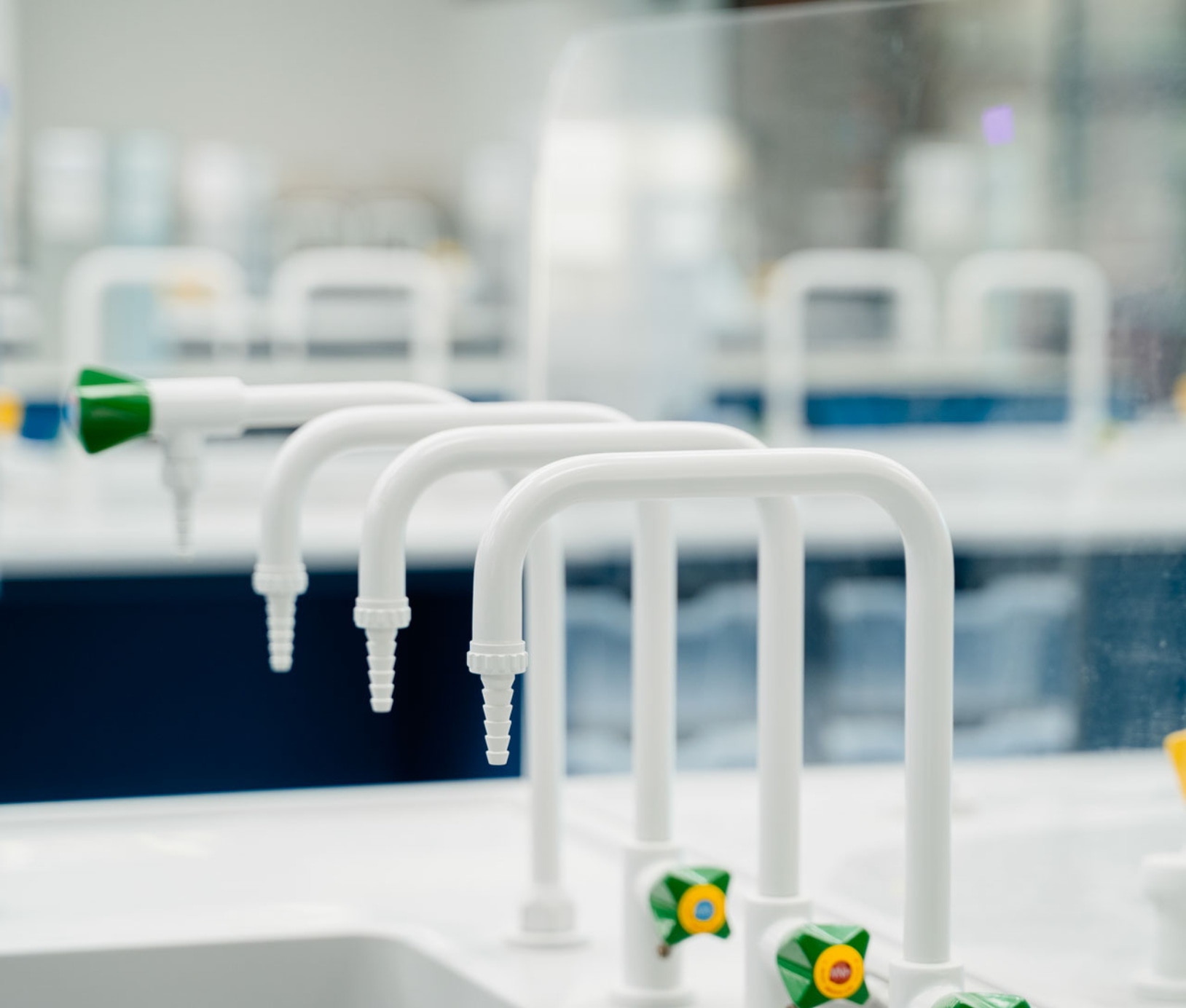
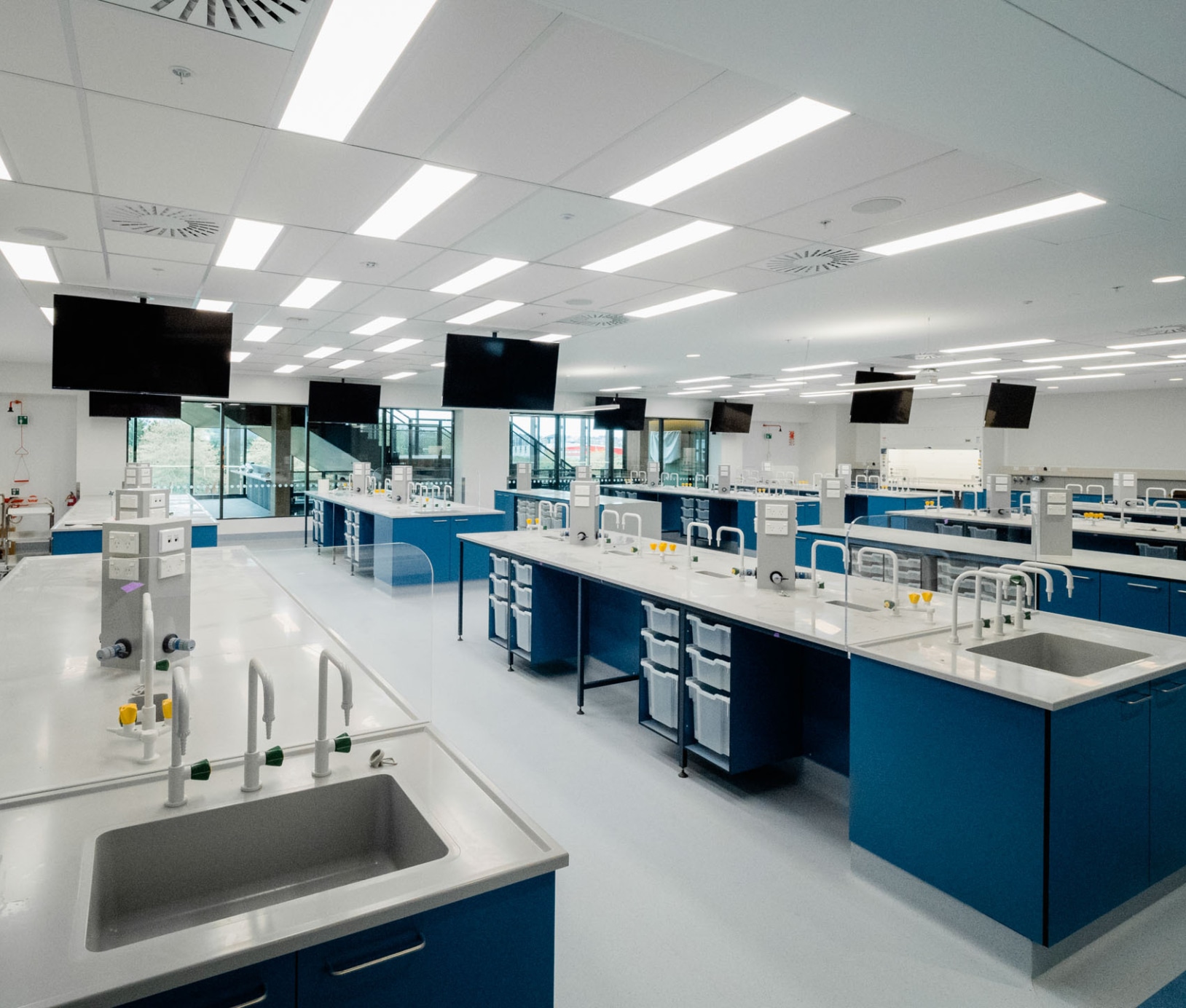