Mon, 13 Jan 2025
Elevating Productivity in Construction and Asset Management
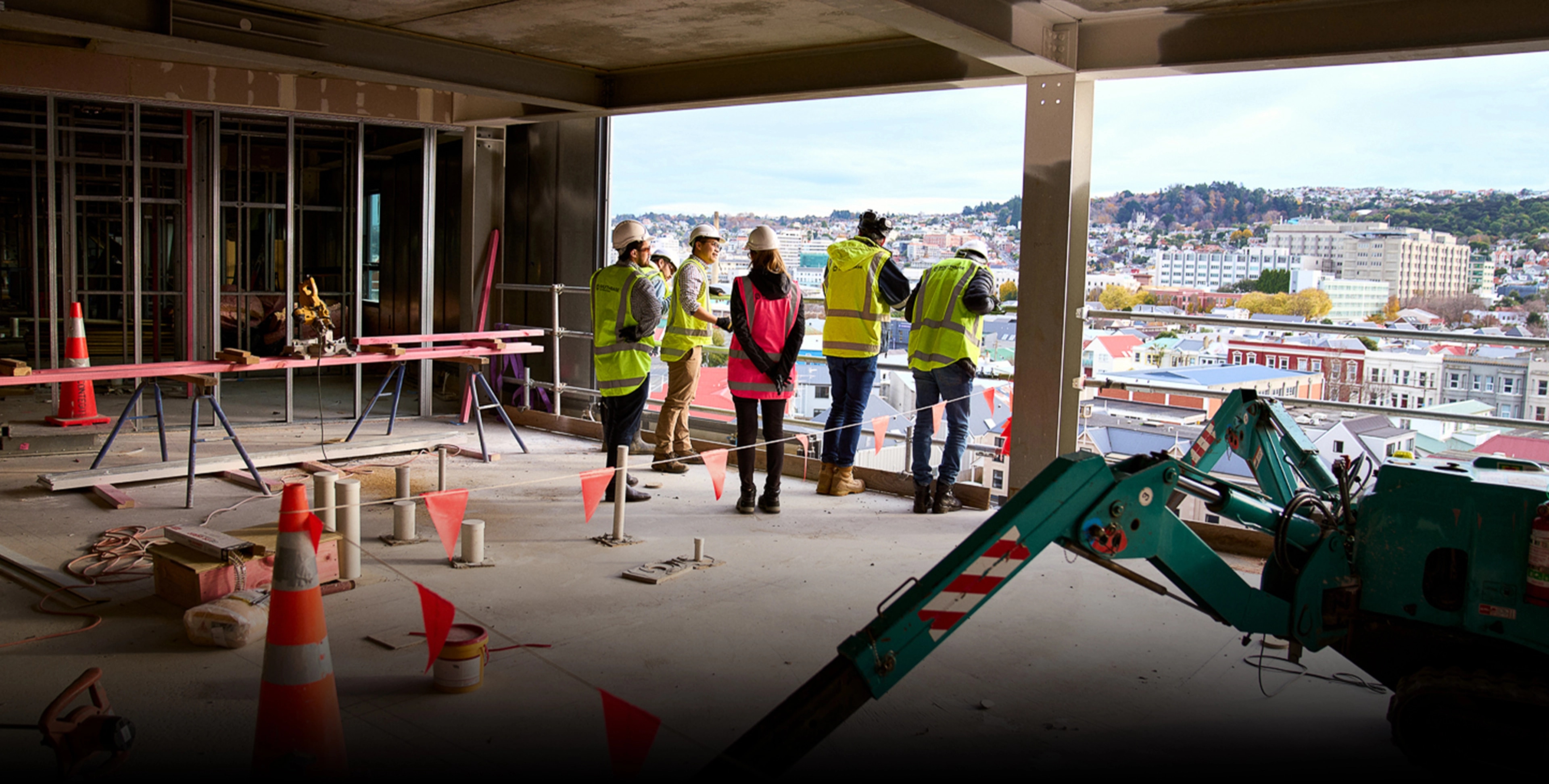
Elevating Productivity in Construction and Asset Management: Ushering in a golden era of growth...
Productivity is a common term, often mentioned when discussing New Zealand's lagging gains. Statistics NZ define productivity as:
a measure of how efficiently capital and labour are used within the economy to produce outputs of goods and services.
A higher productivity rate means a nation can either produce a higher level of goods and services with the same level of inputs or produce the same level of goods and services with a lower level of inputs.
Construction has struggled with productivity, growing only 0.8% annually since 1978 (Stats NZ). Globally, construction productivity improved by just 10% (0.4% annually) from 2000 to 2022, compared to 50% (2% annually) for the total economy and 90% (3% annually) for manufacturing.
From 2020 to 2022, global construction productivity declined by 8 percent. In NZ, labour productivity in construction fell by 1.7%. in the year ending March 2023.
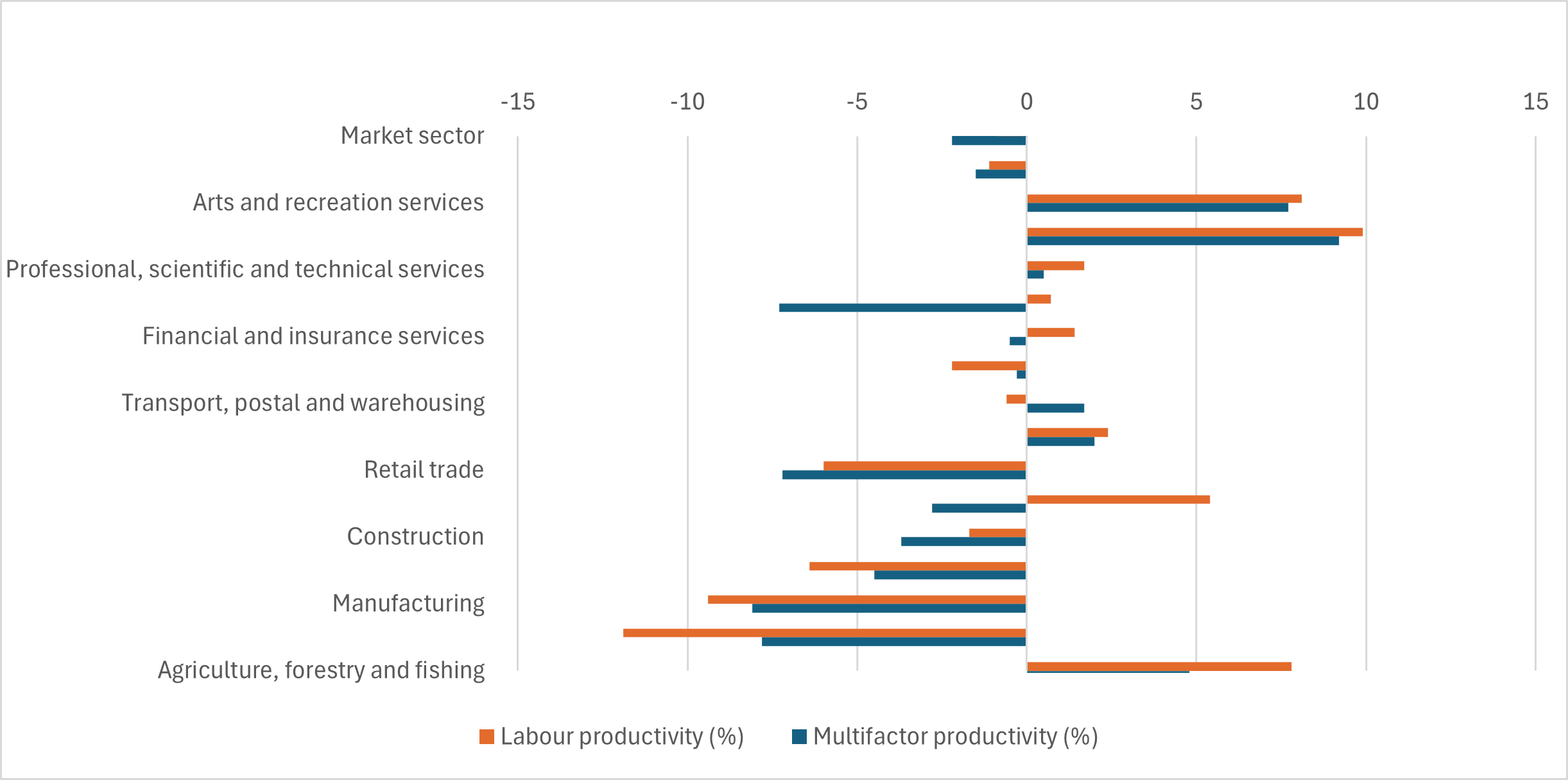
Does Improving Productivity Impact Jobs?
Improving productivity has both positive and negative impacts, particularly on employment. Will it change the jobs that 10% of New Zealanders rely on? Yes, but positively.
On the demand side, we have a growing construction pipeline and a massive infrastructure deficit of construction work (estimated at an additional $200bn over 30 years). With an annual Gross Domestic Product (GDP) run rate of $17.6bn (Ministry of Business Innovation & Employment 2023) and an average 4.3% growth rate (Cordell Construction Cost Index), real construction GDP will double by 2040.
On the supply side, construction employment has grown at 6.3% annually over the past decade, reaching 308,500 workers by June 2023. Without productivity improvements, this number could exceed 850,000 by 2040.
The most optimistic projections for NZ population growth is about 20% through to 2040 (Stats NZ). This means 25,000 new entrants to the labour force each year. At current levels of productivity construction workforce needs will eclipse new entrants in 2028. This could make the constrained labour force and surging construction inflation experienced over recent years a regular feature going forward.
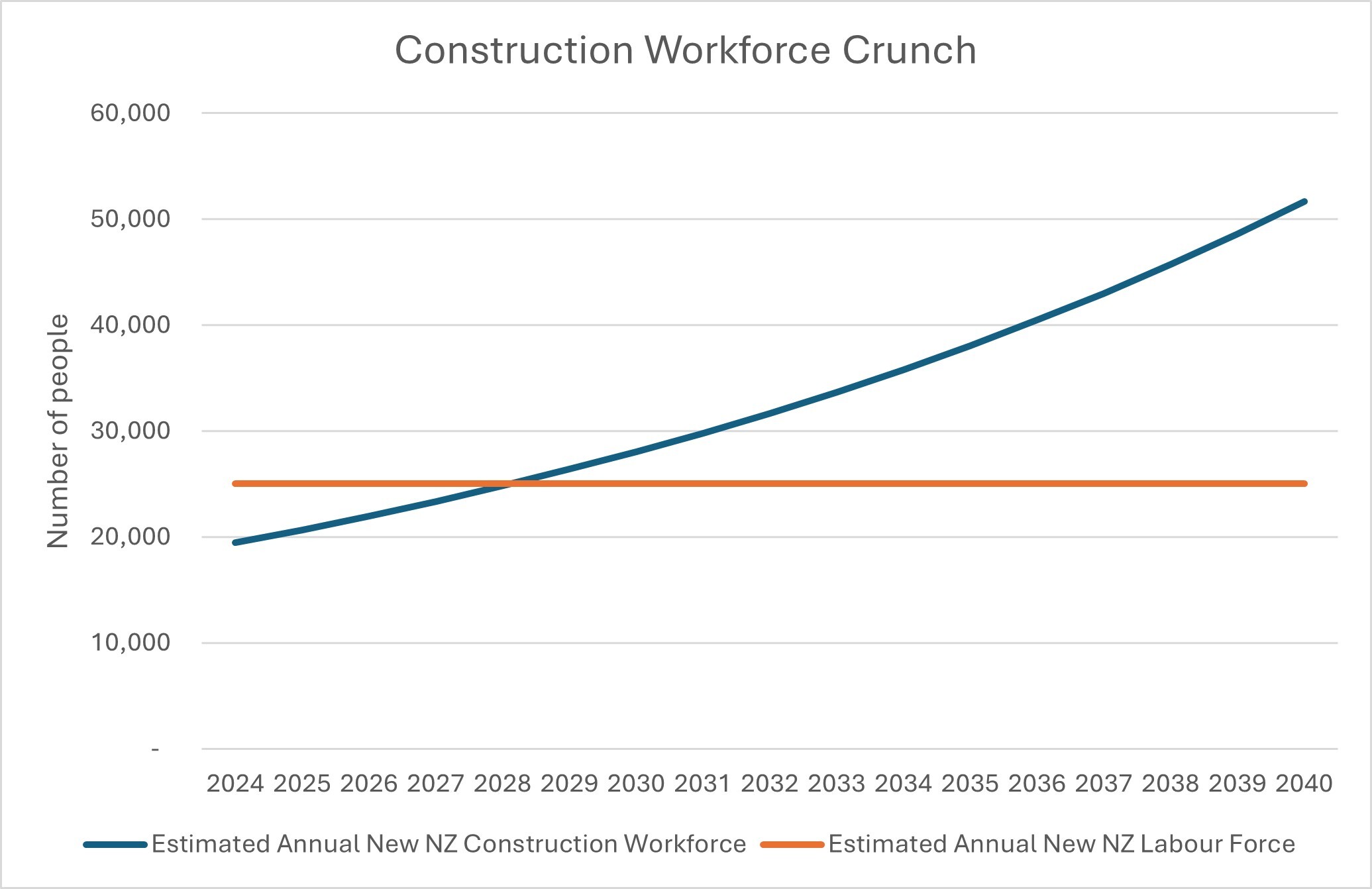
High and persistent construction inflation due to flat productivity gains is unsustainable and will not result in better national outcomes. We must break this cycle by making construction roles more productive, meeting demand without a linear workforce increase. This will also lead to better-paying jobs in the sector.
Changing the Productivity Equation.
Must we accept poor efficiency in NZ construction?
No. We can transform the sector productivity with technology.
The main levers to improve productivity are:
- Technology innovation
- Human capital
- Physical capital
- Competition
- Resource allocation
- Government policies
All these levers are impactful, but technology innovation is underused in construction. Global research shows construction as one of the least digitised industries. Adoption remains slow, focusing on project accountability management rather than driving productivity improvements.
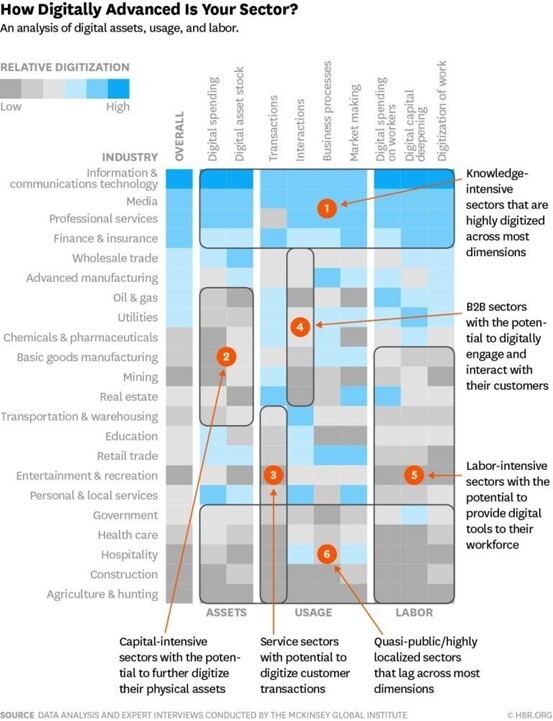
Technology innovation, a major global deflationary force, has dramatically improved productivity in many sectors. Moore’s Law states that since 1975, computer chips double in power every 2 years with minimal cost increase. Technology's impact continues to grow while costs decline.
Can this same technology driven deflationary force be applied to construction?
Yes, and we can prove it.
As an example, we introduced a Hilti ceiling drilling robot into a construction project where it replaced the requirement to have a team of 6 people working for months, at height, drilling holes into a concrete ceiling, with a sole operator. The robot was 2/3s of the time and cost, and produced model based accurate results. This process created secondary productivity benefits of improved health & safety and eliminated onsite measurement and alterations for trades using the drilled holes, saving significant time and cost.
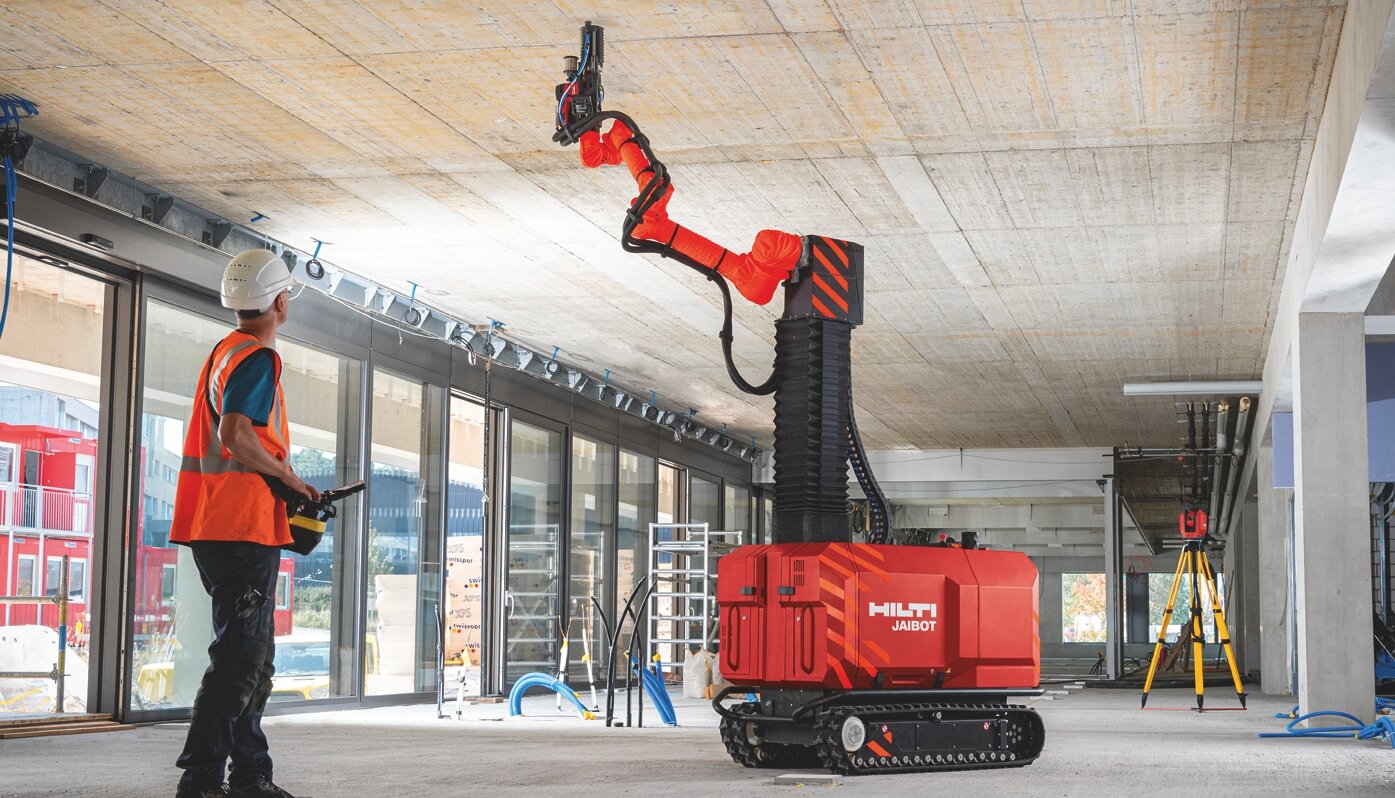
Based on our experience, we can transform productivity in 3 key stages of an asset’s lifecycle:
- Pre-Construction Planning: Digitally model the project before physical work starts to de-risk activities. Collaborative efforts resolve significant design clashes. UK studies report up to 20% cost savings through collaborative modelling and Building Information Management (BIM) processes. Detailed planning created successful projects even before BIM, as seen in the Empire State Building and other examples in How Big Things Get Done.
To prove NZ relevance, we studied the impact of pre-construction digital processes. Resolving design clashes digitally saved $28 in onsite direct costs for every $1 spent. These savings exclude extra costs for management, communication, and delays related to rework or onsite issue management.Ratio of benefits from digital pre-construction
The benefits seen from digital pre-construction processes may be conservative as the introduction of generative AI tools streamline and automate complex and time-consuming processes, such as programme development, cost estimation, risk log and project deliverable management. - Construction Technology Adoption: Construction technologies, such as robotics and reality capture platforms, used through construction add to digital models and create a digital as-built. Reality capture technologies easily record a project as it is built with many Artificial Intelligence (AI) derived capabilities available, such as measuring progress and managing quality. Construction robotics rely on accurate models to operate and will only become more efficient.
- Building “Memory” for Operations: Exiting construction projects with an accurate and relevant digital as-built data set creates the “memory” of a building, an equivalent digital asset to the physical asset. High-level asset operational intelligence use-cases covering long and short-term planning; design, asset operations, capital works & maintenance execution, and verification & assurance, all rely on good asset data.
Unfortunately, 95% of all data captured during construction goes unused or is lost, never able to support improved productivity in asset management or asset lifespan. Studies of the benefits of using data to transition to predictive maintenance programs can reduce annual operational cost by 30-40% and increase asset availability by over 10%. Data is a key dependency in achieving a transition to predictive maintenance and in our experience is largely neglected.
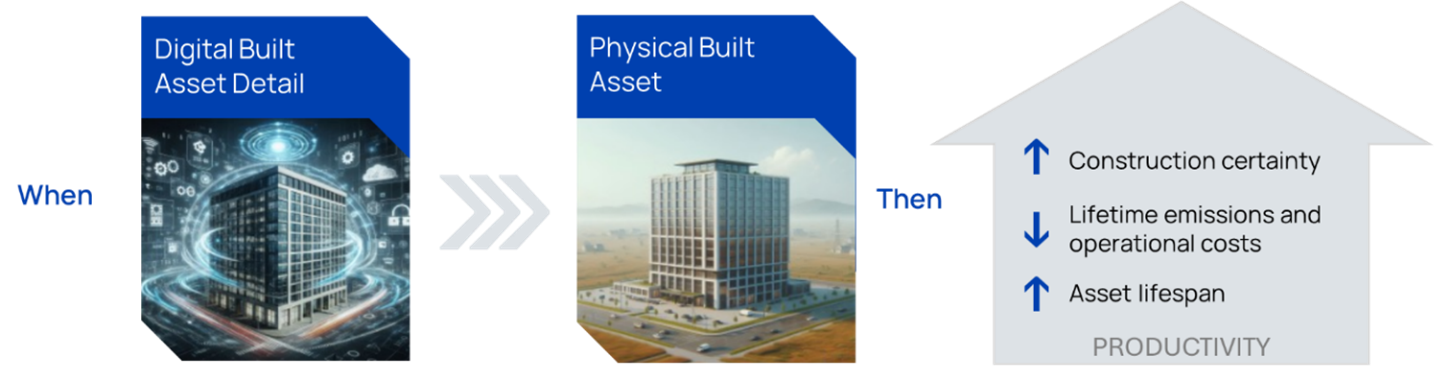
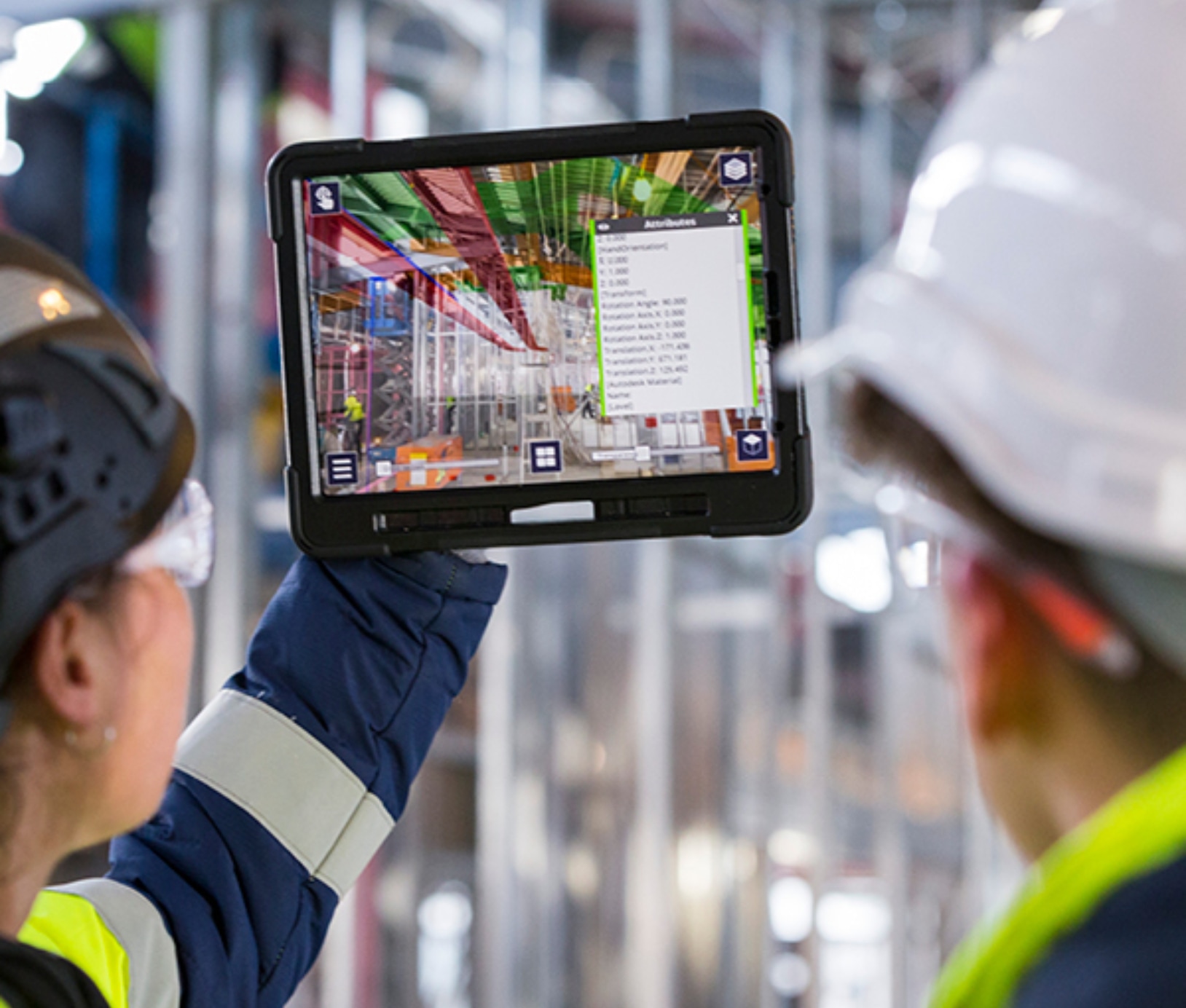
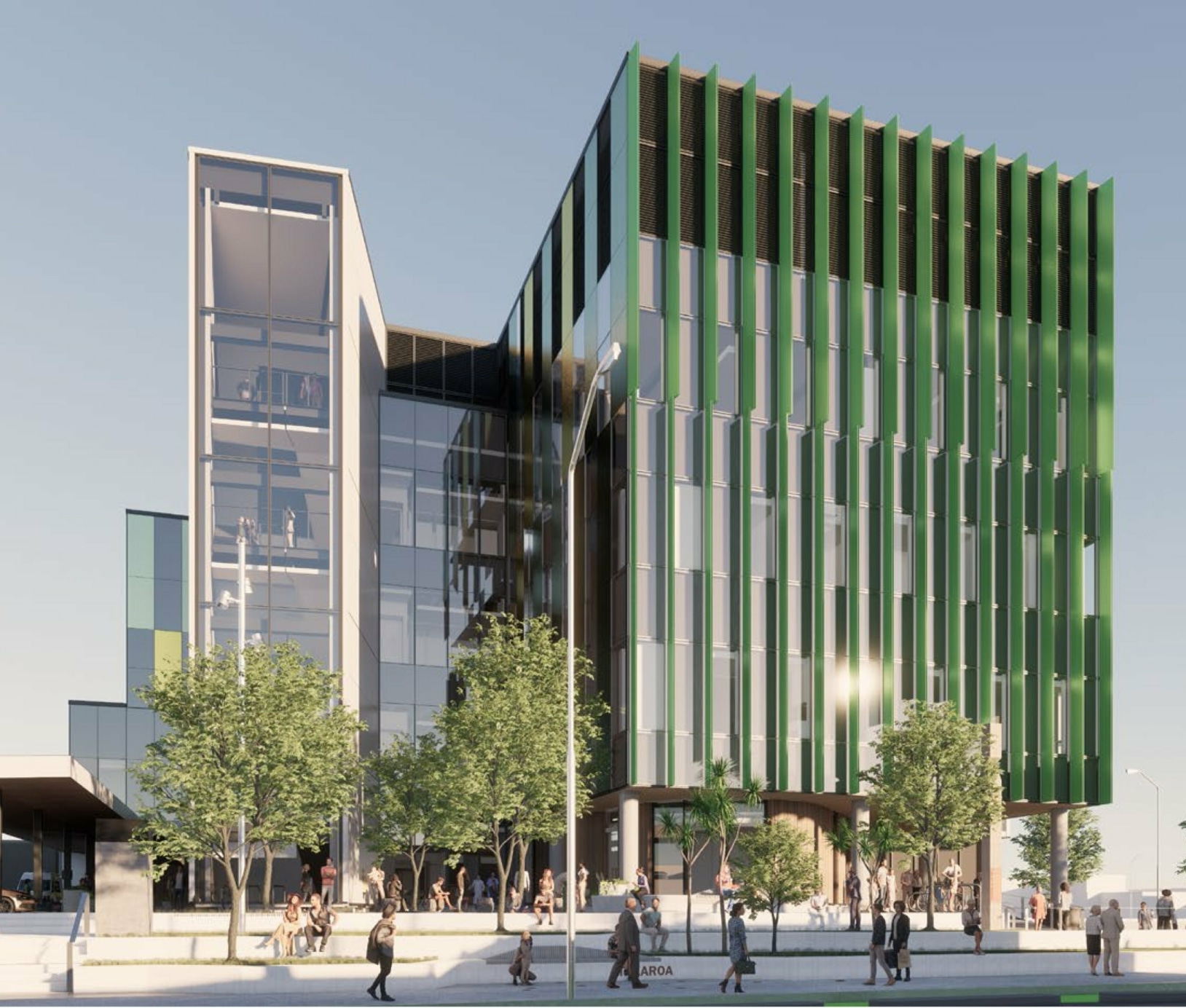
Call to Action
Start your journey towards improved productivity by embracing digital construction methods and capturing valuable data. Here are 3 simple steps to start without large and costly technology transformation programs:
- Adopt a Digital Mindset: Embrace digital modern methods of construction (MMC) to achieve certainty before physical construction begins. Accept some upfront costs to de-risk project time and cost. Investing in digital MMC and BIM tools benefits the entire asset lifecycle.
- Have a Digital Asset Strategy: Understand the value of construction data to your organisation and clients. Create a list of data and formats to capture at each stage from design to operation and asset management. Identify problems to solve within your organisation as future targets.
- Start Simple: Begin specifying and collecting data for every construction project now. AI technologies will compound the value of this data over time by providing simple means of interacting with it. No complex software or digital transformation is needed to start. Just capture and keep the right data.
Improving construction productivity won't happen overnight, and there's no magic AI bullet. It will take small incremental improvements. The good news is that the pieces exist now to make meaningful steps in the right direction.
At Preformance, we're on a mission to transform the construction sector for good. We specialize in Construction Technology and Pre-construction, believing these areas will have the greatest impact.
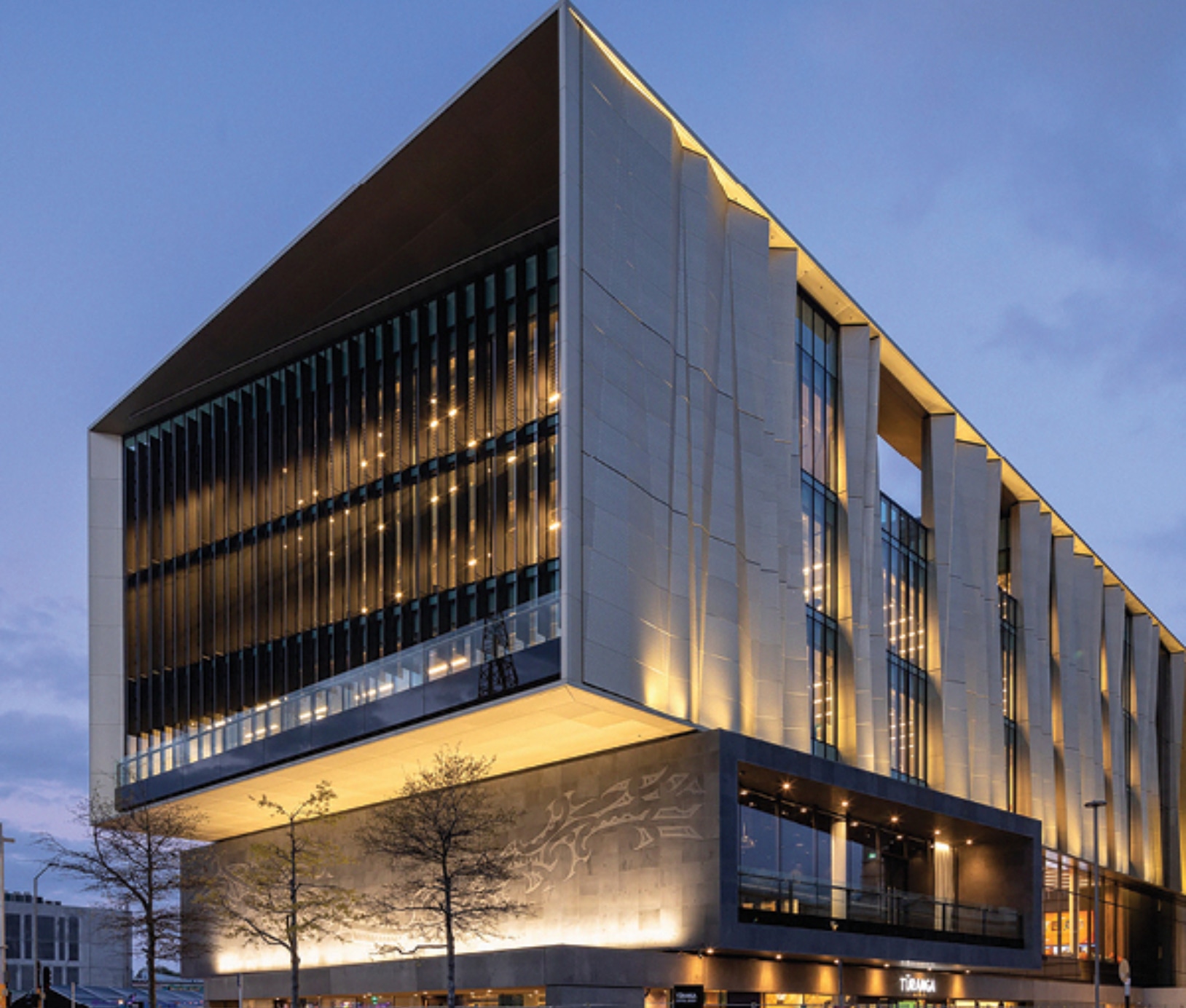
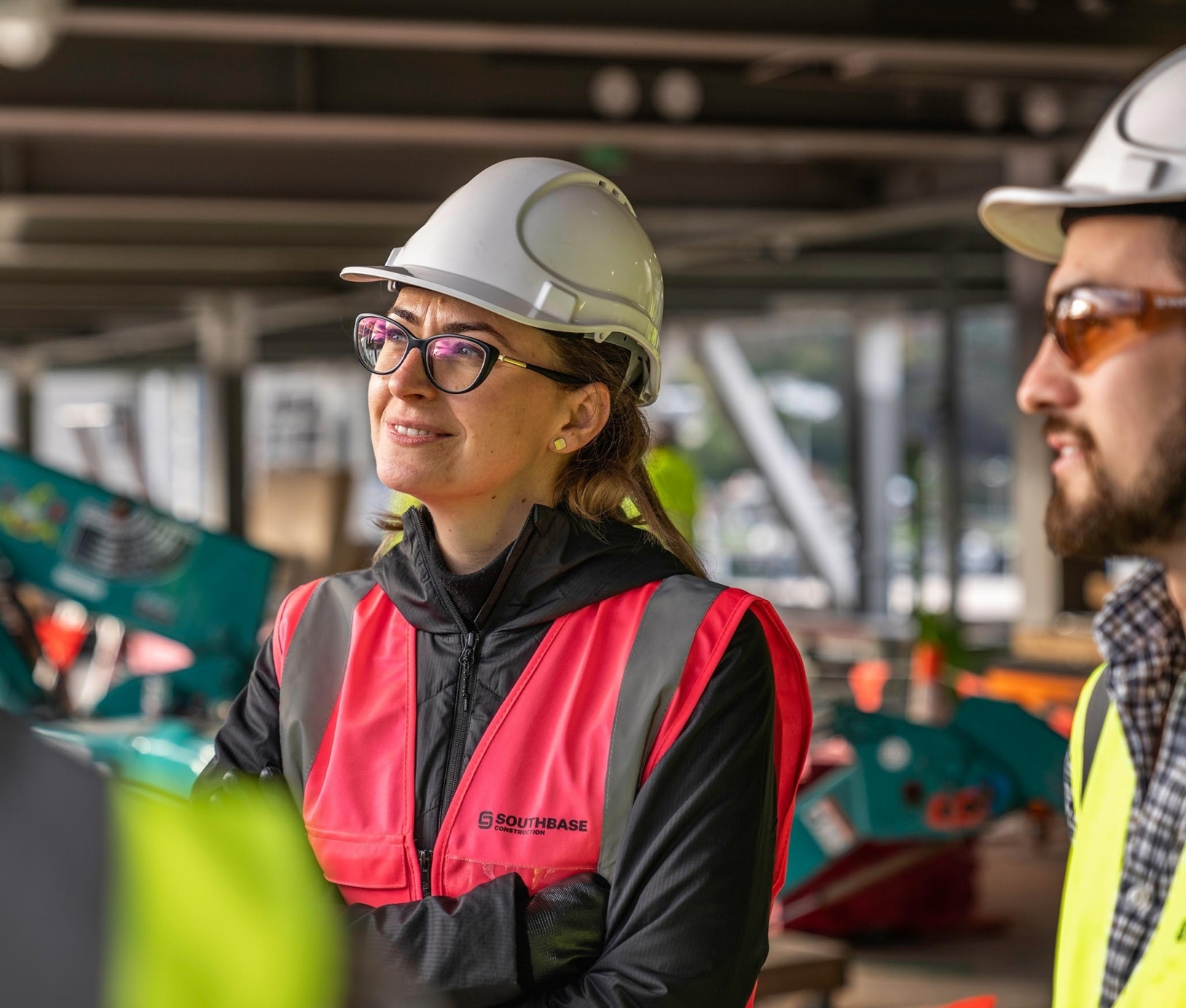